Микроэлектронная индустрия в России (2012)
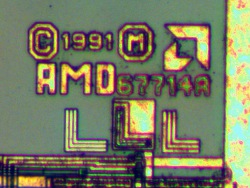
Под катом — драматическая история о пластиковой электронике, российской «гуманитарной помощи» знакомой многим компании AMD и билетах Метро.
Ну и в дополнение — график показывающий как изменялось состояние российской микроэлектроники последние 22 года по сравнению с США и Китаем .
График сравнительного состояния микроэлектроники
Цифры технологического отставания/преимущества — построены «оптимистически»: сколько лет у США/Китая есть следующая технология. Например, у нас с 2012-го года 90нм — у США следующая технология (65нм) с 2006 года, соответственно 2012-2006+1 = 7 лет.Синий график — США, красный — Китай.
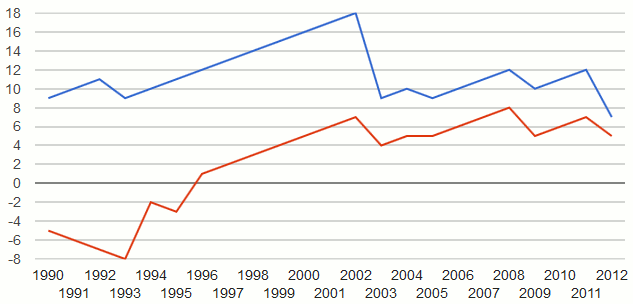
Как я писал в предыдущих статьях — в гонке за удовлетворением спроса на айфоны денег не заработать (если ты не лидер), поэтому в текущей ситуации ничего драматического нет, пока промышленность может производить критически-важную продукцию (а 90нм более чем достаточно для промышленной и военной/космической электроники).
Но нам уже давно пора перестать считать Китай технологически-отсталой страной: по факту они уже много лет впереди нас в микроэлектронике. На данный момент у них запущено производство 45нм, и есть лицензия на 32нм.
Производство микроэлектроники
Ситроникс — Микрон
До 2010-го года Микрон работал по около-микронным нормам, на оборудовании большей частью оставшегося с советских времен.В 2006-м году была куплена технология и оборудование для производства с нормами 180нм (CMOS+EEPROM) с алюминиевой металлизацией на пластинах диаметром 200мм у компании STMicroelectronics. Затем, на базе этого оборудования были разработаны (или куплены — тут данных нет) технологии SiGe (нужно для радиочастотных применений — ГЛОНАСС, радары и проч) и КНИ (для радиационно-стойких микросхем). Объем производства — 1500 пластин в месяц.
В конце 2007-го года однако только торжественно перерезали ленточку, первые тестовые пластины были в 2010-м году. Столь раннее «перерезание ленточки» — исключительно вопрос налоговой оптимизации.
Были сообщения что RFID чипы для билетов метро делает Микрон — однако вскрыв за последние пол года 30 билетов метро — нашел только чипы NXP. К аналогичному результату пришли в августа 2009-го и в компании Chipworks. Впрочем, никакой драмы я тут не вижу, не для метро же покупали это производство. В самом Микроне мои вопросы на эту тему оставили без ответа. Однако одному человеку похоже все-же повезло увидеть микроновский чип 1.5 года назад.
Вот что сейчас внутри каждого билетика метро: (размер — 0.6x0.6 мм)

Затем у той же STMicroelectronics была приобретена технология 90нм с медной металлизацией, требующая дополнительного оборудования (в основном сканеры) с ростом мощности производства до 3000 пластин в месяц:
ASML PAS 5500/750F 248nm/0.7 120 пластин в час
ASML PAS/1150C 193nm/0.75 135 пластин в час (первый в России сканер на длине волны 193нм)
Финансированием занималось Роснано. В сентябре 2012-го — сообщили о начале продаж 90нм продукции. Таким образом, в настоящий момент Ситроникс-Микрон — обладает наиболее современным и универсальным полупроводниковым производством в России, потратив на него очень скромные по мировым меркам деньги.
У Микрона есть младший брат — ВЗПП-Микрон, в Воронеже — там делают дискретные элементы, и микросхемы на микронных нормах.
НИИСИ РАН
Или как его еще называют — «Курчатник». Стоит супер-мелкосерийное производство, степпер — ASML PAS 5500/250С с разрешением 350нм. Объемы производства — считанные пластины в день. Занимаются только военной продукцией, из немногого известного, разработанного и произведенного в Курчатнике — Комдив-64.Интеграл
Долгое время Белорусский Интеграл обладал технологией 800нм, но несколько лет назад наконец смогли запустить 350нм производство на пластинах 200мм, с объемом производства 1000 пластин в месяц. Также есть своё производство «чистых» пластин диаметром 200мм для 350нм линейки.На новой линейке — занимаются похоже только военными микросхемами, а вот на старом гигантском производстве (150mm/800nm — 10тыс пл/мес, 100mm/1.5µm — 30 тыс пл/мес, 100mm/2µm — 15 тыс пл/мес) производят дискретные компоненты и простые микросхемы на экспорт.
Ангстрем («старый»)
На старом Ангстреме — производство с нормами 600нм на пластинах диаметром 150мм (8тыс пластин в месяц) и 100мм, 1200нм кремний-на-сапфире/карбид кремния (4тыс. пластин в месяц).Степперы — Cannon FPA-2000 i1 (длина волны 365nm, NA=0.52, разрешение ~0.5um).
Как и у других отечественных заводов — гражданская продукция идет на экспорт (LED-драйверы, микросхемы управления питанием для сотовых телефонов и прочее).
Ангстрем-Т
Ангстрем-Т уже успел сгенерировать много драмы — потому остановимся на нем подробнее. Проект основывается на корпусе недостроенного завода, оставшегося еще с советских времен. Корпус был построен добротно, и удовлетворял современным требованиям технологии 130нм.Оборудование покупали снятое с Дрезденского завода AMD (130нм, медная металлизация в 9 слоев, 14000 пластин в месяц), а финансировался банкет практически полностью за счет кредитной линии ВЭБа с лимитом 815 млн евро, что в принципе является уникальным случаем – микроэлектронные фабрики редко финансируются за счет кредита более чем на половину. Можно также почитать статью о стройке 2010 года — habrahabr.ru/post/80142/
В 2008-м году заплатили AMD за оборудование ~182.5 млн евро, ~120 млн евро — лицензия на технологию, ~10млн евро — компании Meissner & Wurst за этап А проектирования завода. Однако собственником оборудования стал не Ангстрем-Т, а кипрская офшорная компания Runica. Оборудование в Россию также не повезли, а оставили на складах в Нидерландах и Дрездене, таким образом НДС не пришлось платить ни в Европе, ни в России. Можно посмотреть видео, снятое в тот момент — tv.cnews.ru/?video_id=410
Затем внезапно© финансирование остановилось (показания сторон различаются – толи кризис, толи просрочены платежи по кредиту), оборудование так и осталось за границей (за хранение на спец.складах и страховку теперь также ежегодно нужно платить). По факту – потрачена минимальная возможная сумма, нужная чтобы заплатить AMD – и на этом проект остановился. Кстати, как мы помним, AMD как раз в это время отделяла своё микроэлектронное производство в отдельную компанию (завершилось это в марте 2009), и компания очень вовремя таким образом успешно спихнула своё устаревшее оборудование по очень хорошей цене.
После прекращения финансирования никакого видимого продвижения по проекту не было, только мышиная возня (кто где что на кого страхует, смена собственников и управленцев) и накопление процентов по кредитной линии. В 2012-м году финансирование было возобновлено (впрочем, сообщения о возобновлении финансирования были и раньше), а в конце октября 2012 года — Ангстрем-Т был «официально» куплен Леонидом Рейманом. Одновременно, лицензирована технология 90нм у IBM, которая потребует приобретения дополнительного оборудования. Строительство возобновлено, и запуск производства планируется теперь на начало 2014 года. Безусловно, переход на следующую технологию позволит несколько компенсировать лишние 5 лет, которые оборудование пролежало на складе.
Стоит отметить, что до 65нм таким образом не «заапгрейдить» — 65нм обычно требует 300мм пластин из экономических соображений.
Посчитаем деньги (очень приблизительно) Давайте «на пальцах» грубо посчитаем, как может выглядеть финансовое будущее проекта в самом оптимистичном варианте:
Первоначальный размер кредитной линии на строительство и запуск завода ~ 815 млн евро. Забудем об уже набежавших процентах с 2008-го года.
Допустим, IBM не так жаден, и дополнительное оборудование вместе с лицензией 90нм будет стоить всего 100млн $ (для сравнения, Ситроникс за лицензию 90нм заплатил 27 млн евро если верить прессе).
Тогда сумма к возврату ~ 815*1.29 + 100 = 1151 млн$, ставка 8.5%
Согласно изначальному бизнес плану — расходы на материалы, электроэнергию, воду и газы на производство одной пластины, за вычетом стоимости масок (их оплачивает заказчик) составляют 408.75$. Это наши условно-переменные расходы из расчета на одну пластину, мы их несем только если у нас есть производство.
Годовая стоимость рабочей силы с традиционно низкой зарплатой:
1098(размер штата)*12*30000=395.2 млн рублей в год.
Будем считать, что больше нам ничего платить не нужно (например налогов). Эти 395.2 млн рублей — условно-постоянные расходы, мы их несем не зависимо от того, какой объем производства имеет завод.
График средней стоимости готовых пластин диаметром 200мм на мировом рынке:
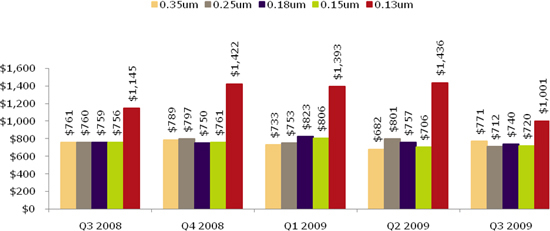
Думаю, будет справедливо считать, что средняя стоимость готовой пластины 200мм 90нм в 2014 году – примерно такая же, как 200мм 130нм в 2009 году. Кстати, обратите внимание на одинаковую цену пластин 350-150нм — так получается из-за того, что кредит за оборудование и строительство давно всеми участниками рынка выплачен, и все работают практически по себестоимости (а труд и материалы стоят примерно одинаково).
Тогда за год завод за вычетом самых основных расходов получит:
14000*12*1001(выручка при максимальной загрузке)-395.2млн рублей/31(условно-постоянные расходы)-14000*12*408.75(условно-переменные расходы на одну пластину) ~ 86.75 млн $
А только проценты по кредиту при ставке 8.5% составят 1151*0.085 ~ 97.8 млн $
Таким образом, даже в тепличных условиях, и 100% загрузке – завод не сможет оплачивать даже проценты.
При списании 50% кредита – по кредиту в этих же тепличных условиях удасться рассчитаться за 13 лет, но в реальности – будет достаточно осложнений (например дальнейшее снижение стоимости пластин со временем, не полная загрузка завода и прочее)
Как проект изначально получил финансирование с такими перспективами? В бизнес плане была заложена оптимистичная оценка стоимости пластин порядка 2000-2500$ + некоторый административный ресурс (т.к. проект все-же был важен для развития Российской электронной промышленности).
Таким образом, без списания кредита, национализации, аннигиляции еврозоны, массивных многолетних дотаций в любой форме (на уровне 100млн$ в год) или ядерной войны на Тайване и Южной Корее — завод работать не сможет. Но наверняка Рейман знает больше чем мы, раз официально ввязался в это дело – остается дождаться 2014-2015 года и посмотреть что получиться.
Другие
Помимо этого, существуют предприятия по-меньше, с производством толще микрона: Экситон, НПО ИТ (для космоса), Восход-КРЛЗ, изготовление фотошаблонов — ЦКП ПКИФ и другие.Смежные производства, попавшие в новости
Plastic Logic
Компания занималась e-ink дисплеями, построенными на основе «пластиковых» транзисторов. Из преимуществ — их гибкость и потенциальная простота изготовления, но электрические параметры пластиковых транзисторов на порядки хуже кремниевых (поэтому никакой революции и убийства «устаревшей» кремниевой электроники не предвидится).В конце 2010-го года Роснано инвестировала в Plastic Logic при условии строительства завода по производству экранов для читалок в Зеленограде.
11 октября 2011 Интерфакс: РОСНАНО увеличило долю в Plastic Logic до 43,8% с 33,7% [...]Оценка Plastic Logic не изменилась, инвестированные средства полностью пойдут на строительство завода в России, сообщили в РОСНАНО.В начале 2012-го года внезапно© компания решила, что момент упущен, и завод строить больше не выгодно. Компания будет теперь заниматься только разработкой и лицензированием технологии (впрочем, кому теперь это лицензирование нужно, если рынок завален).
Строительство завода по производству некремниевых дисплеев в Зеленограде планируется начать в декабре текущего года. На предприятии будет выпускаться около 100 тыс. дисплеев в месяц.[...]
Epic fail.
Crocus Nano Electronics
17 мая 2011 Пресс-центр РОСНАНО: РОСНАНО и Crocus Technology создают производство MRAM — впервые в мире по технологии 90 и 65 нм РОСНАНО и Crocus Technology, ведущий разработчик магниторезистивной памяти, сегодня объявили о заключении инвестиционного соглашения о создании в России производства памяти MRAM следующего поколения. Общий объем сделки составляет $300 млн. В рамках соглашения РОСНАНО и Crocus создают компанию Crocus Nano Electronics (CNE), которая построит в России завод по производству памяти MRAM средней и высокой плотности с проектными нормами 90 и 65 нм с применением технологии термического переключения (Thermally Assisted Switching — TAS), разработанной Crocus.Однако это не полноценное 65нм производство (300млн$ это копейки для полноценного 65нм производства) — будут брать готовые CMOS пластины (с транзисторами и металлизацией), и наносить слой для магниторезистивной памяти. Подождем 2013-го года и посмотрим, что у них получится.
GS Nanotech
25/ 09/ 2012 РИА Новости: Центр по производству компонентов микроэлектроники заработает осенью под Калининградом Первое в РФ крупносерийное предприятие по производству компонентов микроэлектроники по топологии 45 нанометров и менее, Центр GS Nanotech, расположенный в Калининградской области, войдет в строй в конце осени, заявил журналистам начальник производства центра Алексей Ярцев.Если походить по их сайту, то сразу видно, что компания занимается только резкой пластин, корпусировкой и тестированием микросхем. Т.е. на входе — готовые пластины, на выходе — микросхемы. Это безусловно тоже важное дело, но «45нм» — тут вообще никаким боком к предприятию не относится.
MAPPER Lithography
Роснано вложил 40 млн € в технологию безмасочной литографии. Это на мой взгляд — самое вкусное вложение денег Роснано. Безмасочная литография — это будущая революция в мелкосерийном производстве микроэлектроники (прощай FPGA), и особенно это полезно для производства военной микроэлектроники: теперь для производства 10 микросхем не придется заказывать комплект масок за 150-500 тыс $, или ждать десяток «соседних» проектов, чтобы напечататься на одной маске и одной технологии производства.Суть технологии MAPPER — экспонирование электрон-резиста лучем электронов. Это делалось и раньше, но теперь — лучей не 1, а 13'260. Таким образом одна установка сможет экспонировать от 1 до 10 пластин в час, что вполне достаточно для многих мелкосерийных продуктов.
Разработка микроэлектроники
Отмечу наиболее интересные, на мой взгляд, отечественные разработки, не покрытые завесой секретности:МЦСТ
МЦСТ-R500S (500Мгц SPARC 2 ядра)Эльбрус-S (500Мгц, своя архитектура)
МЦСТ-R1000 (1Ггц SPARC, 4 ядра)
ЭЛЬБРУС-2С+ (500Мгц 2 ядра Эльбрус, 4 ядра DSP)
Элвис
1288ХК1Т (МF-01) — 4-х канальный SDR-приемник1892ВМ5Я — 1.2GFLOP DSP (32-bit)
1892ВМ10Я — 4 GFLOP DSP (32-bit) с поддержкой ГЛОНАСС
Миландр
1986ВЕ92У/MDR32F9Q2I ARM Cortex-M3 128kb flash/32kb SRAM, 80MhzК1986ВЕ21У/MDR32F2QI ARM Cortex-M0 128kb flash/16kb SRAM, 36Mhz
НТЦ Модуль
1879BM3 — 4 8-битных ЦАП, 300 МГц, 2 6-разрядных АЦП 600Мгц, 150Мгц процессорное ядро и интерфейс внешней памятиNM6406 — 300MHz DSP (2 32-bit MAC за такт)
КМ211
К5512БП1Ф (Кварк) — 150Мгц 32-х битный RISC процессор, изготовлен на Микроне по 180нмРезюме
Российская микроэлектроника в последние годы существенно ожила — как в плане производства (90 и 180нм на Микроне, 350нм на Интеграле), так и разработки.Сейчас уже есть возможность разработать и произвести абсолютно любую промышленную, военную и космическую продукцию — процессоры, микроконтроллеры, силовую электронику, радиационно-стойкие микросхемы, микросхемы для радиосвязи, ГЛОНАСС и радиолокации. Но как мы помним, разработка — это дорогое удовольствие, поэтому сделать все сразу не получится.
В микроэлектронике нет «устаревшего» производства, продукция по любым нормам имеет свой рынок и цену. Даже советские заводы до сих пор работают на экспорт — выпуская микросхемы питания, дискретные элементы (силовые транзисторы и диоды) и прочую мелочевку — а мы их потом покупаем в материнских платах и сотовых телефонах под зарубежными торговыми марками.